Ketley Brick’s Richard Dyer
I work for Ketley Brick and PMI were kind enough to sponsor me on the 2019 ICTa Study Tour of Germany. I would firstly like to thank you for selecting me as your candidate and I hope you’ll be pleased to hear that I found the entire experience incredibly valuable in my development and understanding of different methods of clay manufacturing. I would also like to thank all of the individuals involved in the organisation of the tour as it was perfectly put together with each venue providing a wide variety of information and insight into their respective specialisms.
Throughout the week we visited 4 clay brick manufacturers. 3 of these manufacturers produce insulative clay blocks and 1 makes facing bricks and pavers. Each manufacturer uses different raw materials and insulating methods which they were very forthcoming in the explanation of. It was very interesting to see how their methods vary even though the end product is intended to produce very similar properties. For example, each insulative brick manufacturer uses a different type of insulation (rockwool, polystyrene, woodchip and fibreglass) for which different processes and machinery are required to insert. They also use different clay mixes to improve the thermal and sound insulation of the block itself. Although the methods used were varied, there was a very strong theme that ran through the visits. This was that the emphasis on maintenance and replacement of machinery was a very high priority. They schedule the replacement of their machinery rather than waiting for it to require repair work which although expensive in the short term, allows them to produce more consistently and with fewer employees required for upkeep. I think there is a lot that I can take away from this ethos as it is now apparent to me that running equipment until breaking point is not necessarily the most cost efficient way of getting the most out of production.
The 2 equipment manufacturers that we visited, Lingl and Keller, gave a great insight into the technology and innovation that is being utilised in modern production methods. Again, both of these companies have a strong emphasis on efficiency and also pay a great attention to the specifics of their customers’ requirements. Both companies had departments that analysed the raw material used by their customers at a very high level of detail. This allows them to tailor each piece of equipment precisely to their clients’ needs and pushes the boundaries of what can be achieved with each raw material. Having seen the possibilities generated by these companies, I am keen to see how they can assist me with future product development.
We also visited Grothe who manufacture glazes and engobes for bricks and tiles. Their site is very clinical as they are storing large quantities and varieties of minerals to mix together. It was very interesting to see the possibilities that they can open up in the design and alteration of products. To me, the most valuable part of this visit was seeing the level to which they quality control each and every product that is manufactured. All of their materials are tested before, during and after every production run to ensure the highest standards of quality. They also store samples of every colour that they make to ensure absolute consistency if the customer requires more.
In conclusion, the theme that is common to all of these visits is that German clay manufacturing puts a huge emphasis on maintenance, consistency and quality control. This seems to work very well for them and I hope that I can utilise my learnings in improving how we operate at Ketley Brick. I think that with such a stark contrast in operating procedures, we are never going to work in completely the same manner as I saw in Germany but I believe that small changes can be made to make us overall more efficient.
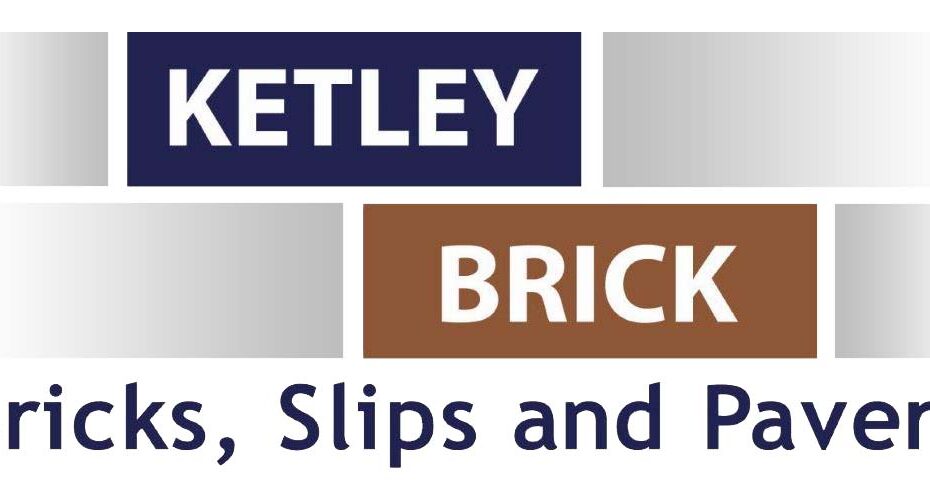